The Cold Spray CNC Machine
The machine is set up in four basic system components:
- High Pressure Air Compressor
- Nozzle Particle Delivery System
- The Targeting System
- Powder Recycling
The Cold Spray CNC Machine
The machine is set up in four basic system components,
1. High Pressure Air Compressor and dryer designed for continuous 500 PSI.
2. Nozzle Particle Delivery System. Within the nozzle assembly, metal particles are injected into the high pressure air stream and accelerated to “supersonic speed” through a small orifice. This creates an output velocity between 600 and 1000 meters a second (Mach 1.7-9). When the particles impact the target location, the high kinetic energy causes them to instantaneously bond, forming a part through successive layers of 30 micron particles. If the metal particles are too slow the metal bounces off the target; too fast the metal smears, erodes, or splits in to smaller particles. When conditions are right, a part is formed, at near 100% density and has properties very similar to billet material.
3. The Targeting System is typically a plate connected to a robot arm or other CNC positioner. The robot arm moves the plate in front of the spray nozzle to build a shape, layer by layer. The particles fuse while hitting the target substrate plate and then begin to build on top of one another. Successive robot motion creates the desired shape of the complete part. As a comparison this method of printing is significantly faster than existing than powered layered fusion process and is similar in speed to robotic welding, but without the unpredictability that results from melting a metal.
4. Powder Recycling; simplistically it is a Dust Recovery Collector, designed to control
residue particle material for recycling savings and environmental control.
Benefits & Applications
Cold spray works with many alloys, most easily non-ferrous metals such as Aluminum and Copper. This provides common and inexpensive alloys, that are perfect for replacing many casting, manifolds, braces and brackets, pulleys and heatsinks.
Dock Umbrella Holder
As we add more sophistication of design in our products, we look for new manufacturing methods that can produce economically and accommodate multiple design constraints. Sometimes thinking outside the box allows exploration of materials and shapes that will accommodate innovative improvements in products, such as improved cooling in heat sinks, to the use of copper for medical applications for its natural antibacterial properties.
If you are interested in a visit to see the machine or get a quote on a part, contact Protomatic, Doug Wetzel.
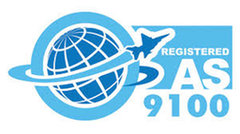