Feature
3D printing: a naval manufacturing disruptor?
Although 3D printing is making an indelible mark on defence, the innovative process is forever limited – the technology fills gaps in conventional manufacturing, but it will not surpass it. John Hill reports.
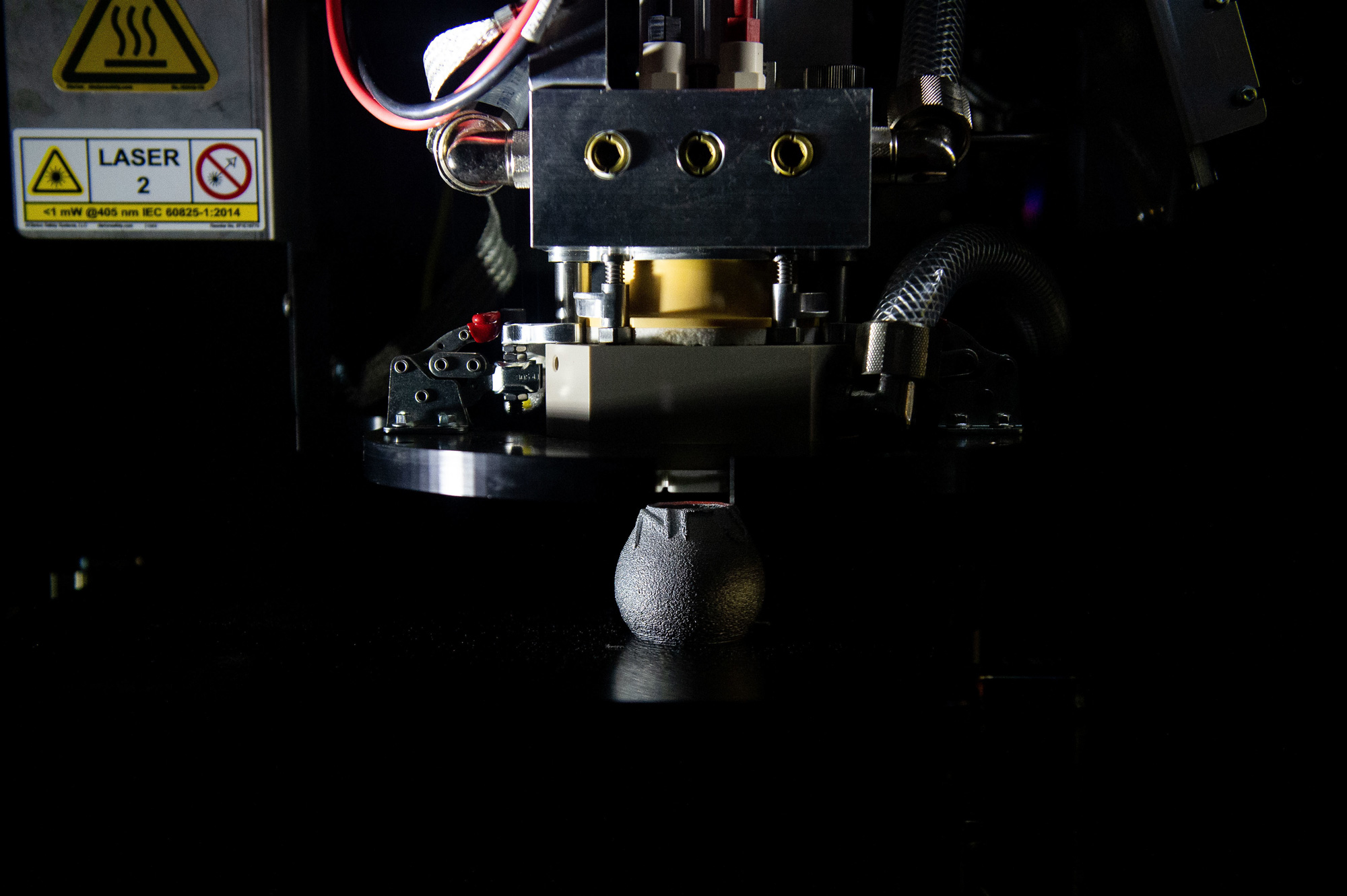
A 3D printer conducts a test print aboard Wasp-class amphibious assault ship USS Essex (LHD 2) during Rim of the Pacific (RIMPAC) 2022. Credit: US Navy/Mass Communication Specialist 3rd Class Donita Burks
With all the emerging technologies that are available these days it has become commonsensical to transition to a more efficient way of doing things. Take for instance artificial intelligence: it has the potential to autonomously process everything across all industries. However, some technologies, while highly disruptive, only go so far in making life a little easier.
Upheld as a disruptive technology in manufacturing since its creation four decades ago, 3D printing – or Additive Manufacturing (AM) as it is also known – is a process not so easily integrated into existing manufacturing and production techniques.
The process of making a physical object based on a three-dimensional digital model by layering materials in succession has provided defence producers custom tools and parts alike. This new method has its limitations; not so much based on inherent problems with the technology itself, but can be on the reluctance from users to adopt, and adapt to, emergent capabilities.
Among the difficulties for AM if that it lacks certification and has an inability to produce at considerable volume. At the moment, AM is used to produce custom tools and components for industry that require fast delivery times and/or customised manufacturing.
A US Navy spokesperson told Global Defence Technology that “with 3D printing, ideas from the workforce can be rapidly designed and prototyped and placed into action providing for safer and faster accomplishment of maintenance and modernisation tasks”.
However, if the process is to surpass conventional manufacturing, then users undergo a fundamental change of culture to increase AM infrastructure. The market is there, with GlobalData estimating that AM will be worth $70.8bn by 2030, having grown at a compound annual growth rate of 18% between 2021 and 2030.
This projection indicates that while AM is limited to filling the gaps in conventional manufacturing and playing a supportive role in that way, the sector is still a promising and profitable manufacturing method. So, what makes AM so valuable as a supporting role?
The naval industrial base is an ideal place to apply AM as shipbuilders can 3D print tools and parts when needed as opposed to ordering items and waiting for them. This conventional route will extend pressured delivery schedules – the US Government Accountability Office has already complained that the US Navy lacks insight into its schedules for its submarine programmes since shipbuilders have not conducted a schedule risk analysis.
The Navy recognised this in November 2022, when the service decided to install a 3D printer on board its ships, namely the USS Bataan (LHT 5), so that personnel can perform technical services in response to issues while in operation thus securing a credible level of readiness and self-sufficiency.
Elsewhere in the naval construction community, other industry players have also explained how AM fits into their methods, and why the technology will only go so far as it relates to conventional manufacturing.
There is no transition, only delivery assurance
Speaking with Global Defence Technology, Ian Brooks, technical director of Additure – an AM producer based in Warrington – said: “We always say, as an industry, we’re never going to replace conventional manufacturing, we’re just going to help.”
Additure fills a gap in conventional manufacturing when components may be lacking.
“That might be because they’re legacy parts, it might be because of damaged parts, you know, the full plethora.
“Sometimes the numbers don’t quite stack up with conventional manufacturing. There may be an order quantity of ten. But our minimum order quantity for it to be viable in the conventional supply chain might be 500. So, we're able to navigate that a little bit with 3D printing.”
We always say, as an industry, we’re never going to replace conventional manufacturing, we’re just going to help.
Ian Brooks, technical director at Additure
At the Defence Security and Equipment International (DSEI) 2023 exhibition in September, Additure showcased the work it has done for UK defence prime Babcock. It is only through partnerships such as this one that smaller, emerging and innovative companies can access the UK’s defence market.
“I think the immediate barrier that we faced was a resistance from the MoD [UK Ministry of Defence] to deal with SMEs [small-to-medium-sized enterprises]. But generally, the entrepreneurial stuff and the innovative stuff is coming from another tier down: the start-ups. So that cut out a lot of the innovative additive manufacturing,” Brooks said.
“So we then had to scramble around to try and grab onto the coat tails of a prime that currently has a contract with the MoD.
“I think there’s a lot of reasons why 3D printing isn't maybe getting traction in the defence industry. But I think first and foremost, the MoD as an entity needs to think how it can engage with SMEs more easily, while still making sure that they've done all their due diligence.”
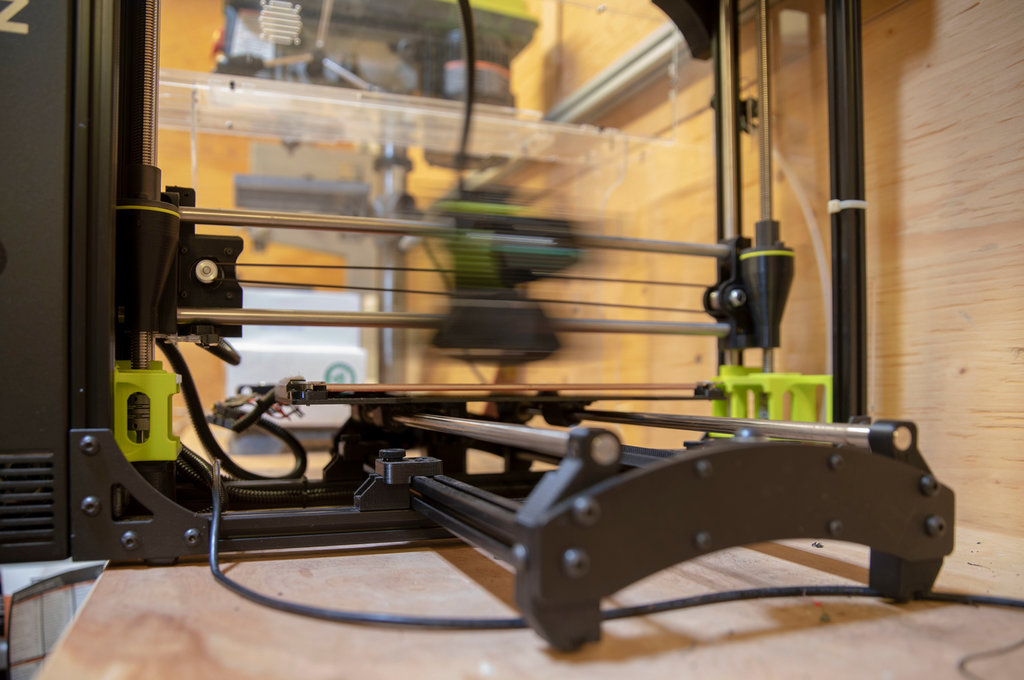
A 3D printer produces a piece of equipment at Naval Station Mayport’s Southeast Regional Maintenance Center (SERMC) in 2021. SERMC provides surface ship maintenance, modernisation and technical expertise in support of the ships and facilities on base. Credit: US Navy/Mass Communication Specialist 3rd Class Austin Collins
By partnering with Additure, Babcock can use effective and sustainable technological methods while moving production closer to the point of need. In a recent Additure press release Brooks added that “in any global supply business, it is crucial that the right materials and spare parts are in the right place at the right time” – this is where AM comes into play.
Perhaps the next shift is one of mindset, and, instead of thinking of AM as an emerging technology that the defence industry must transition towards, view it as a disruptive technology that is sought after for assured delivery.
Or, as the US Navy put it more succinctly, “the [US] Navy sees AM as a means to compliment traditional manufacturing more than naval builders ‘transitioning’ from legacy to AM processes.”
“It’s learning for us; it’s learning for them”
Difficulties in naval sustainment supply chains in the US have also created difficulties for a service looking to generate as many sea days as it can from its hard-pressed fleets. The submarine sector in particular is struggling to overcome severe delays due to a range of technical and administrative issues.
Bartlett Maritime (BM) – an Ohio-based corporation that assists the US Navy in the resolution of the capacity and capability shortfall in the sector, supporting both submarine construction and maintenance – has recently entered a strategic supplier agreement, employing the services of a local AM producer named Additive Engineering Solutions (AES).
This agreement will develop large format polymer additive manufacturing products such as assembly fixtures, jigs, and custom shipping containers.
David McCall, president and COO of BM, said one of the things that companies such as AES can provide are component-specific solutions.
“We can quickly make the fixture as the tradesman works on it. If it’s not exactly right, we can quickly get that fed back to our supplier and they can either modify that fixture and can make it better and more efficient for the worker.”
It’s easy for them to come get eyes on the target and see exactly what the problem is, which really helps in the turn-around and the design of either the shipping container or even, more importantly, the fixture.
David McCall, president and COO of Bartlett Maritime.
McCall also explained that the proximity between their businesses in Ohio is also a key asset in trialling BM’s integration of AM.
“Since [AES is] new, they’re on the cutting edge, but also they’re local, they’re out of Akron [a city near BM], and it’s a local business so we can quickly get the product back and forth.
“Sometimes it’s very good if you have a problem and you’re trying to co-operate together to solve it. It’s easy for them to come get eyes on the target and see exactly what the problem is, which really helps in the turn-around and the design of either the shipping container or even, more importantly, the fixture as we tried to do various type of repairs on components.”
Bartlett Maritime’s approach sees the company integrating AM methods where tools, parts, and equipment are needed, and unaccounted for outside the mass production of conventional manufacturing methods. This process is being refined all the time.
“Part of the strategic partnership we have with AES is that it’s learning for us; it’s learning for them,” McCall emphasised.
AM materials “need to find their place within defence”
There is more to finding the capability integration solution than educating the market about ways to integrate AM, it is also about learning the applications of certain AM materials. In addition, it is less about the overarching theme of AM and more about where the wide range of specific AM materials are best suited within the defence industry, as Brooks explains.
“So, we have two technologies here, laser powder bed fusion, and WAAM – Wire Arc Additive Manufacturing, and that will fill a niche. But there are many, many other 3D printing technologies, not just in metals, as well, obviously, in polymers. If you look at the umbrella of technologies that call themselves ‘3D printing’, how many are there? 20, 30 maybe,” Brooks said.
“What I think is that those technologies need to find a place within the defence industry. What I mean by ‘place’ is that when will those technologies and where will those machines and processes actually sit?
What I think is that those technologies need to find a place within the defence industry.
Ian Brooks, technical director at Additure.
“Some might be more suited to field-based deployment, some might be forward operating versus some might be back in battalion base. I think that’s where we need to start and I think over the next three to five years, you'll see those technologies start to establish themselves in those locations.”
However, there are signs of openness and a growing ambition to exploit AM at a greater volume and in more complex ways. The US Navy, for example, plans on scaling capabilities by deploying AM equipment where it improved maintenance operations, stated the US Navy spokesperson.
“In parallel, the Navy is working to activate an industrial base able to utilise AM to produce components in support of new acquisition shipbuilding and in-service ship and submarine maintenance,” the spokesperson said.
Scaling production while also filling the gaps in conventional manufacturing is the sort of major cultural change that will market the AM process more widely across defence. However, the key point is that filling gaps and scaling production go hand in hand.
Certification and cost requirements for AM products
There are a number of additional aspects to consider when integrating AM manufacturing process; namely gaining certification for parts, especially components used on board submarines and surface vessels, as well as the higher costs incurred compared with conventional manufacturing.
McCall explained: “It all boils down to how you certify a part. That’s going to be the long pole in my mind. You put the file in there, you can construct the part, but how do you know it’s going to function in the environment? What is the non-destructive testing? What is the certification process?”
When asked about existing regulations to AM products, the US Navy noted that “the absence of AM specifications makes the production method difficult to implement”.
The spokesperson added that “overcoming [this challenge] will enable scaled AM production in support of ship and submarine new construction and maintenance operations.”
Instead, in lieu of AM-specific guidelines, “Navy AM will meet the same regulations and/or certifications imposed on traditional fabrication methods, such as fire hazards, hazardous material (explosives/toxicity), light emission, etc.”
AM is a means to augment and de-risk these supply chains, accelerating the pace that needed parts are produced and delivered to the Navy.
US Navy Spokesperson.
“The rigour behind the certifications for AM processes differ based on the criticality of the components under consideration. Of note, Technical Publications have been published for qualifying two metal AM processes (Laser Powder Bed Fusion, Directed Energy Deposition); each follows a similar qualification approach to traditional methods such as casting and forging.”
Meanwhile, another consideration when integrating AM is the cost, which is often more than ordering and waiting for products that have been cast and forged.
“So cost is a difficult question, because we are new,” Brooks added. “These are new processes. They’re not as mature as the conventional technology. So generally, we are more expensive.”
This question comes to the heart of the value of AM and its supportive role in filling the gaps in conventional manufacturing.
The US Navy points out that the ship and submarine building industrial bases are suffering from long lead times for castings, forgings, and other traditional manufacturing processes, while “AM is a means to augment and de-risk these supply chains, accelerating the pace that needed parts are produced and delivered to the Navy.”
“Forget about the cost of the part,” Brooks continued. “What is the cost of not having the part at all? And I think that’s where we can fill because if the conventional route cannot provide that part and the part is needed, the cost question almost goes out of the window.”