The role of SMEs in military manufacturing
By Oliver Shepherd, chief operations officer at Subsea Craft
Throughout my career in the Royal Navy, I have been in situations where I have been extremely grateful for technological advances in the defence sector. These may often have been as a consequence of gradual upgrade or improvement to existing capabilities. However, I also understand the need for recombinant innovation: learning and combining existing and complimentary capabilities to make a new product — one more suited to addressing emerging needs and threats.
Historically, the defence sector has always featured at the forefront of technological innovation, and right now there is a significant area of opportunity in digitisation, specifically in harnessing it to optimise our technology. Designing today’s marine equipment in a digitised way and creating a digital twin to support the manufacturing process allows organisations to test, qualify and learn, whilst a standardised digital thread connects the twin to the physical build. This also allows development at pace, all the time cognisant of budgetary considerations and maintenance needs.
Small and medium enterprises (SMEs) are well equipped to help navigate this technology, being nimble in both innovation and creation of new assets, which further benefits the defence sector.
The digital thread is a digital library of information, assets and data that stretches from the concept to finished product.
We use the digital thread to optimise each interaction throughout the product life cycle, for example from conception, design and manufacture through to in-service support, training, asset management and evaluation. Each of these steps, in developing a concept into a physical product, produces strands of digital activity and information — and collectively these strands are known as the digital thread.
This thread is a digital library of information, assets and data that stretches from the concept to finished product. The value of this is having a collaborative design and development tool that is fast becoming standard in many production sectors, providing value and cost reduction.
The utilisation of the digital thread throughout the design optimisation phase allows for the completion of a ‘single source of truth’ about any of the systems, sub-systems or components being developed at any time. This allows for development as a virtual team and supports fast-pace innovation and problem solving. In the manufacturing phase, the use of the digital thread allows for the faithful translation of the final design into the intended product.
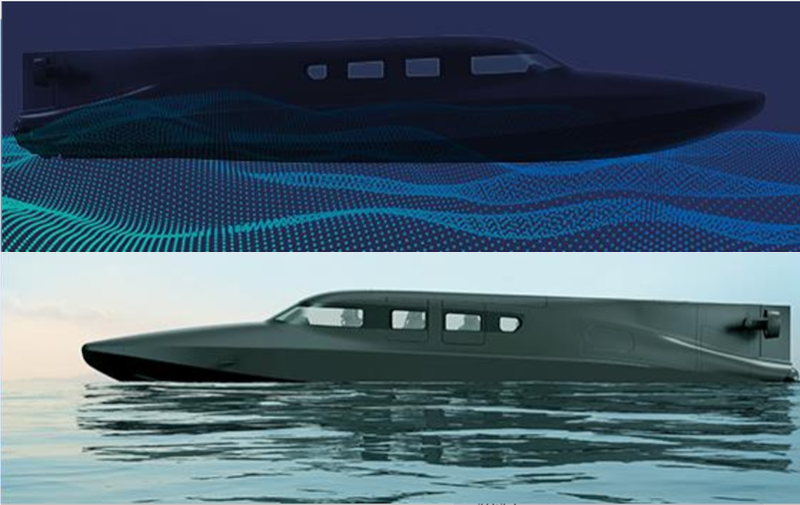
// Digital twin technology illustrated. Image: Subsea Craft
During the service life of a vessel, such as our next-generation diver delivery unit, VICTA, the digital twin supports individually tailored, pre-provisioned maintenance and upgrade work based on data captured from the vessel directly. We’ve found an increased reliance on modelled simulation can be developed within VICTA’s digital twin, enabling modifications, developments and upgrades to be brought into service with minimal disruption to asset availability and improved levels of safety evaluation.
This doesn’t come without its challenges, however. Digitisation and full use of the digital thread is held back in the defence sector by concerns about data sensitivity, logistics and control of data distribution. This is compounded by the lack of any formalised standard for the implementation of a digital thread into complex programmes with multiple collaborators. A common digital environment for the defence sector is a solution to this problem but is still a long way off. Circumventing this issue with bespoke, product specific options is a viable model for SMEs in the immediate future.
The digital thread and twin concept represents a significant opportunity for industrial advancement, similar to the introduction of the electric motor to replace steam engines during the Third Industrial Revolution. Much is still to be done before the full value can be seen across the sector - notably, standardisation of definitions and frameworks that will allow confidence in data capture.
Teaming the know-how of our thriving UK tech industry with our exemplary military and special forces personnel makes for a progressive approach to this solution finding.
Organisations must also be mindful of cognitive bias. Ex-military operations specialists will provide considerable value in the design and creation of new defence technologies; however, this must be balanced with the scrutiny of outside industry experts. Teaming the know-how of our thriving UK tech industry with our exemplary military and special forces personnel makes for a progressive approach to this solution finding.
It is this collaboration of experts in individual fields that enables the development of a truly innovative technology that is fully fit for purpose. Using machine learning in a digital twin allows for the continued development and modification to meet different operational employment options.
In today’s economic climate, so significantly hit by the global pandemic, it is vital to provide ever more flexible solutions for defence operations. Not only from a budget perspective but from a multi-purpose point of view. If, for example, one craft can deliver against three separate operational objectives, it is, by definition, providing value. When that is coupled with world-class innovation and game-changing technology the real opportunities can be seen.
There is significant scope for this type of digital innovation in the maritime industry with recent events forcing far more streamlined and tightly run processes. The use of a digital twin is just one part of the many steps that can be taken to realise the value of recombinant innovation in the defence industry.
Oliver Shepherd is chief operations officer at Subsea Craft with experience across the defence, intelligence and humanitarian sectors. As a Royal Navy mine clearance diver and high-threat explosive ordnance disposal officer he has worked, managed, and commanded across the spectrum of land, maritime, and joint operations. Specialising during the latter part of his uniformed career in intelligence, he gained unique insights into government and international strategy during positions within defence and national intelligence agencies. He has contributed to several international disarmament programmes in the humanitarian sector, and as the director of operations at Subsea Craft he is focused on innovation and optimisation.
Comment