Land
Map the Gap: Dstl’s competition to help the British Army cross water
The UK Defence Science and Technology Laboratory is running a competition to explore ways to help UK Armed Forces map the wet gaps that may slow down operations. Norbert Neumann talks to Dstl and its industry partners about the experiments.
During land operations, one of the most challenging obstacles militaries face is wet gaps. Rivers, canals or streams can significantly hinder operation speed, and thus campaign success. Traditionally, in the UK, Royal Engineer reconnaissance troops carry out surveillance of waters and banks. Most current methods are slow and involve the demanding use of manual or low-tech equipment.
The Map the Gap competition was launched in February 2020 by the UK Defence Science and Technology Laboratory (Dstl) on behalf of the cross-government Defence and Security Accelerator (DASA) team. Phase one trials began earlier this year with five suppliers, and solutions for the second, current phase, will be demonstrated in Germany in February 2022. Lessons learnt there will support future British Army procurement decisions.
The gap
The competition set out to investigate how remote and autonomous platforms could improve exploration by increasing reliability and tempo of measures whilst limiting potential risks to personnel in the operations. In August 2020, DASA awarded a £1.3m contract to five companies to develop semi-autonomous reconnaissance and survey systems for the first phase of the project.
Dstl senior engineer William Taylor says: “Phase one of Map the Gap tasked suppliers with capturing key measures of potential river crossing sites. These included ground bearing capacities, gap width, difference in bank height, bank profiles, river-bed profiles and water flow rate, all to be captured remotely or autonomously whilst ensuring the data could be easily interpreted and delivered.”
The collected information can be used to determine optimal river-crossing locations and enhance decision-making regarding bridge or ferry planning. These tasks required the development of new sensors to meet new requirements and the installation of those alongside existing sensor capabilities into robots.
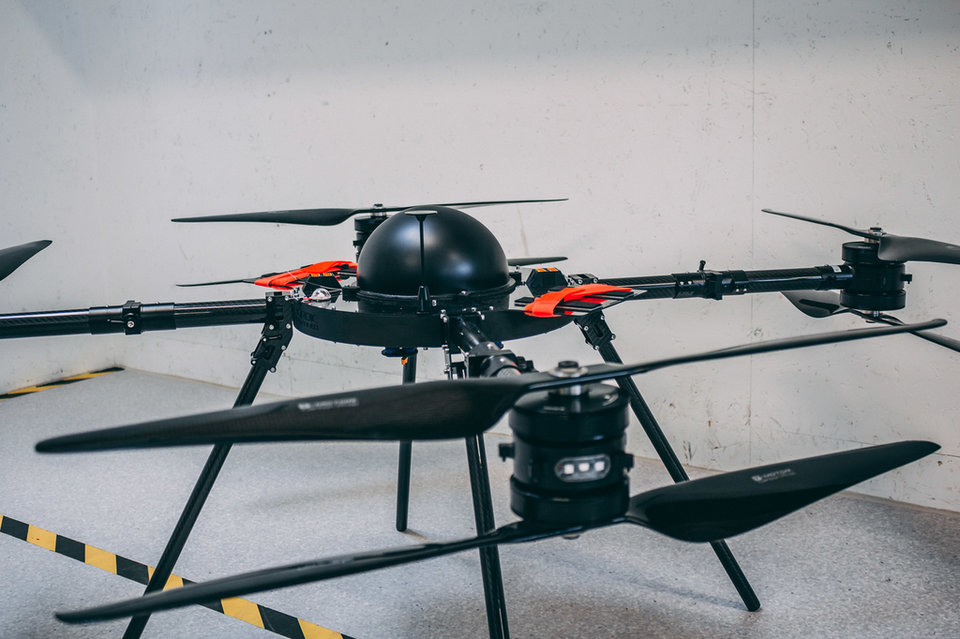
// Credit: Nordic Unmanned
Phase one
Norway-based remotely piloted aircraft system specialist Nordic Unmanned was one of the companies demonstrating capabilities during the first phase. Using its £272,656 funding, the company demonstrated uncrewed aerial system sensors, data exploitation and a semi-autonomous capability for engineer reconnaissance.
The company also describes itself as an integrator of solutions. Nordic Unmanned vice president for infrastructure Jose Luis Gil Yepes says: “If there is a customer, in this case, DASA and Dstl, we look at their needs, find a solution to that need, break that down into components and then integrate them into our platform to provide a final result.”
Nordic Unmanned equipped its foldable Staaker BG200 quadcopter drone with a light detection and ranging (LIDAR) sensor and a WaFlow sensor. WaFlow is a ball-shaped instrument that measures water depth and water flow speed. The sensor communicates with and sends collected data to the uncrewed aerial system and the ground base while floating.
Nordic Unmanned, however, was unable to demonstrate the maturity of its solution and could not perform ground-measuring capabilities during the trials, and therefore has not been selected for the next phase. “The LIDAR was an off-the-shelf-sensor but was a bit immature. It required more testing, data acquisition and more tuning,” says Yepes.
Another candidate of the first phase was a British marine robotic expert Wight Ocean in partnership with US-based amphibious and militarised crawler system provider C-2 Innovations (C-2i). Additionally, British ocean and earth science researcher body the National Oceanography Centre, which has experience in ground and underwater robotics, served as a science advisor for the developer. Wight Ocean received £309,282 in funding.
C-2i’s bottom crawler served as the base platform for phase one of the project, with suitable technologies further developed and integrated to meet DASA’s requirements, such as soil-strength measurement.
“We knew of off-the-shelf sensors that would do the other measurements that they wanted,” Wight Ocean director Graham Lester explains.
“The core itself was really cleverly designed in that it could do most of the challenges in its standard configuration. Getting a profile, crossing the actual gap itself, getting the data on the [water and bank] profiles or getting data on water depth.”
We will be able to rapidly grow both our military and commercial offerings
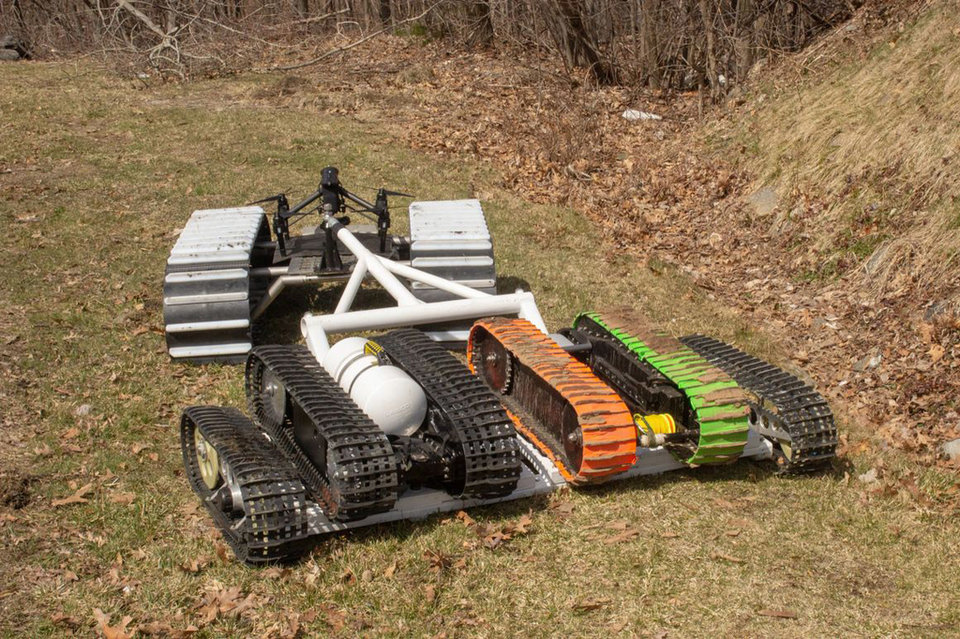
// Wight Ocean and C-2i submitted an amphibious crawler to the competition. Credit: Wight Ocean
In this phase, the partners focused on having the correct configuration for all of these tasks and adding adequate sensors to the platform.
Despite its efforts, the company did not receive further funding to participate in phase two of the competition.
Lester recalls: “The team that was doing the evaluation wanted a really nice and easy user interface, which we thought was not really part of the challenge and we saw that as something we could easily do in phase two.
“We felt it was more important to show something that actually did the job. We focused on, not necessarily making the data pretty and quick to get, but to make sure that we could actually get it.”
Out of the five companies, only the UK-based uncrewed robotic manufacturer Digital Concepts Engineering succeeded with its sensor-equipped uncrewed ground vehicle and drone team.
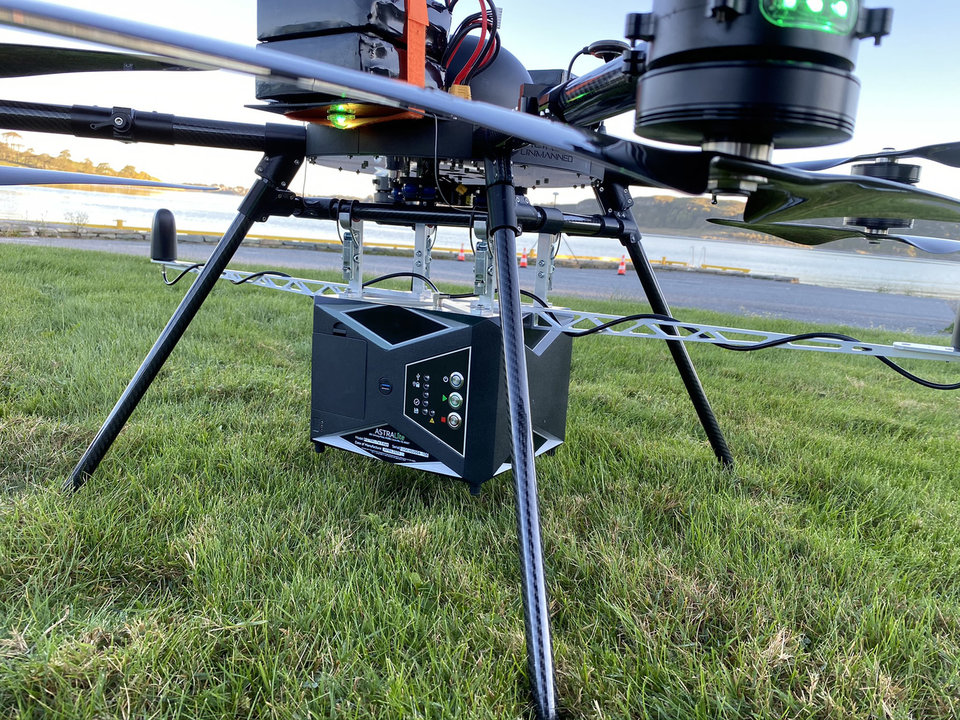
// Credit: Nordic Unmanned
The next steps
Concluding the first experiments, the requirements for the wet gap challenges became clear for Dstl and DASA.
“It was clear that each concept and platform type showed potential [in phase one], however, it became apparent that each of these platforms would be best utilised in different ways. This resulted in phase two seeking to develop and refine concepts of operation for these different systems to understand how they can best be used for engineering reconnaissance,” says Taylor.
In February 2021, after successful demonstrations, Dstl and DASA announced the allocation of £2m in funding for phase two of the Map the Gap project. Besides Digital Concepts Engineering, two industry partners that did not participate in the first phase of the competition, ISS Group and Ultrabeam, will develop and showcase their solutions.
This phase aims to “incorporate greater levels of autonomy and refine solutions to a higher technology readiness level,” Taylor says. DASA’s ultimate vision is to map wet gaps without putting personnel in harm’s way.
// Main image: Nordic Unmanned demonstrated uncrewed aerial system sensors during the first phase of the Wet Gap competition. Credit: Nordic Unmanned