We design and manufacture our own tanks from aluminium, stainless steel or carbon steel plate to fully equipped tanks. The tanks are automatically welded and tested through radiographic checks on the welded joints, pressure test, capacity measurement, safe loading and brake tests. Next to that, the majority of the equipment going from frame work to electrical, pneumatic and hydraulic equipment is designed and built in-house.
Stokota follows the latest available technology for the most safe operations of their units. Refuellers and dispensers are dealing with flammable, volatile substances in an already dangerous environment. The majority (70-90%) of incidents and material damage is due to human error, either caused by the operator or by third parties. With as result human trauma and severe damage of equipment.
PROVEN HERITAGE IN A WIDE RANGE OF SOLUTIONS
Food supplies shipment
THE MOST COMMON INCIDENTS ARE:
Faulty handling or actions done by the operator
Faulty repairs done by technicians due to (too) complex installations
Driving or maneuvering in the vicinity of an aircraft
Bonding not adequately executed
Intake line damaged by third parties, damaging intake hose, pit coupler, pit valve,…
Failure of filter elements due to poor readout by operator
Use of incorrect materials and equipment (ATEX, CE, EMC, MID, ADR, …)
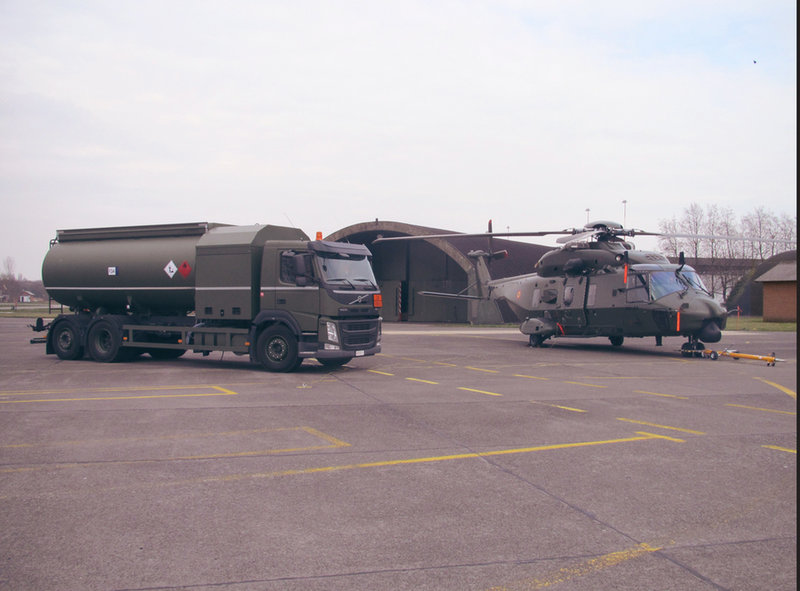
TO ELIMINATE/REDUCE THE RISKS OF INCIDENTS, MEANING WORKING AT A HIGHER SAFETY LEVEL, STOKOTA USE THE LATEST INNOVATIONS ON REFUELLING EQUIPMENT AND THE BROAD USE OF SENSOR TECHNOLOGY.
The use of a Human Machine Interaction. The system, like the electronic counter, monitors all steps. No start of the fuelling if the setup sequence is incorrect or incomplete. Automatic fuel stop on system errors. Driving away after refuelling prohibited automatically if the wrap-up is incomplete.
Reduce the risk of a collision with aircraft or other ground equipment by using proximity sensors.
Reduce failure in the on-board control system by simplifying the different electric and pneumatic steering. For this Stokota uses can-bus systems and a PLC-free control system. It reduces wiring failures and eases largely maintenance and service.
FWS – electronic ∆p system. Monitoring, calculation, indication and controlling the fuelling operation in relation to the ∆p is done automatically. The ∆p is automatically and continuously recalculated to the max. flow. This is programmable per filter vessel type. Resettable with user password or badge system with different user levels (operator, maintenance, manufacturer).
System records when (option: and who) there was a ∆p reset in the system logbook.
Bonding is checked by monitoring system. An interlock on the bonding clamp to see if the clamp is in use is not telling you anything about the bonding itself. Therefore we are checking the resistance, continuously. If OK, fuelling can start or continue. In case of a failure, fuelling is prohibited or stopped.
To avoid mistakes in fuelling the correct airplane, we are using the FTL-protocol for communication between the back-office and the refueller/operator.
Largely available but not commonly used, is an operator identification system. Stokota is able to implement a RFID tag system to login to the refueller prior to start his job. It is also used to set different grades of operations allowed. Maintenance for example have higher rights than an operator. All these logins, actions, … are stored in the logbook, which cannot be erased.
Another feature which is highly cost-effective is the use of an automatic start/stop system of the truck’s engine. Activating the deadman switch results in the start of the engine, engaging the PTO, automatic setting of the correct speed. After refuelling stops, all is reversed. Such action results in huge saving of gasoil, and consequent fuel costs.
A refueller works only as good as the operator and other personnel is familiar with it. Stokota finds it crucial to give excessive training by its engineers to the end-users, to the into-plane companies. As well operators, as supervisors, maintenance people, …
Use of correct material and equipment acc. ongoing standards
The above shows Stokota is concerned about the safe operation of a refueller, as well for the operator as for the surrounding equipment, by using the latest state-of-the-art equipment and by installing widely sensor technology.
Last but sure not least, the aim of Stokota is to be a partner for our customers. From the very first stage of a request till after the delivery.
A strong partnership is a win-win situation for both.
Contact details:
Dijkstraat 23
B – 9160 LOKEREN
Tel: 0032 9 349 17 18
Fax: 0032 9 349 17 25