Feature
Hybrid theory: the development of armoured alternative propulsion
Common in the civil sector, hybrid drive vehicles could offer range of benefits in the military domain. Samuel Cranny-Evans reports.

The Abrams X concept, unveiled in 2022, included the potential for electric drive integration in main battle tanks. Credit: Richard Thomas
Hybrid electric drives (HED) for the commercial market are so familiar that they are hardly remarkable, with the quiet whine of a family saloon, or even a bus pulling away from traffic lights, is probably familiar to most.
However, the HED is almost completely absent in armoured fighting vehicles (AFV) and main battle tanks despite offering obvious benefits like significant levels of onboard power to help run active protection systems, mission systems, and, in the not-too-distant future, computers running artificial intelligence algorithms on the front line.
There have been several attempts to explore HEDs in a military context, indeed, some of the very first tanks used a form of electric transmission. United Defense integrated hybrid drives into vehicles like the M113, M2 Bradley, and AAV7 from the 1960s and there were multiple periodic attempts at developing hybrid electric vehicles (HEVs) throughout the 1990s and 2000s.
The UK’s Future Rapid Effects System from the early 2000s was expected to employ a HED, and the Swedish SEP modular armoured vehicle (Splitterskyddad enhetsplattform) developed by BAE Systems from 1994 came in tracked and wheeled variants with HED. The concept is therefore far from new but has not been accepted into service.
Greater interest in the technology driven by efforts to reduce military carbon footprints and developments in the commercial world may be the key to unlocking hybrid technology for defence.
Design and benefits
There are two different types of HED; a series HED is powered by converting the output of a petrol-powered generator into motion at a number of electric motors. It generates fuel saving advantages when the vehicle can maintain steady speeds and little or no variability in power demand. This is because the internal combustion engine that powers the motors is able to operate at its most efficient and provide the greatest range for the spent fuel.
A parallel HED, combines a conventional mechanical drive train with electric motors; the motors might provide additional power and torque when the vehicle is in its low range, thereby improving acceleration. This can reduce fuel demands by providing additional power when the rolling resistance is highest – i.e., when the vehicle is stationary.
There is also evidence that HEDs can improve vehicle mobility. A study from Japan’s Acquisition, Technology and Logistics Agency (ATLA) showed that a series HED fitted to a tracked vehicle weighing 13 metric tons was able to accelerate from 0 to 56 km/h in around 15 seconds, making it 12 seconds faster than the M113 on a road. Its top speed was also 10% faster than an M113 at 73 km/h and it even achieved a 40% fuel efficiency.
It was able to climb a 60% gradient at 5 km/h thanks to the large amount of torque (2,034 Nm) generated by the electric motor. If this kind of performance can be replicated across vehicles, then it is reasonable to assume that the many trials and concept demonstrators being pursued around the world will build a body of evidence supporting HED adoption.
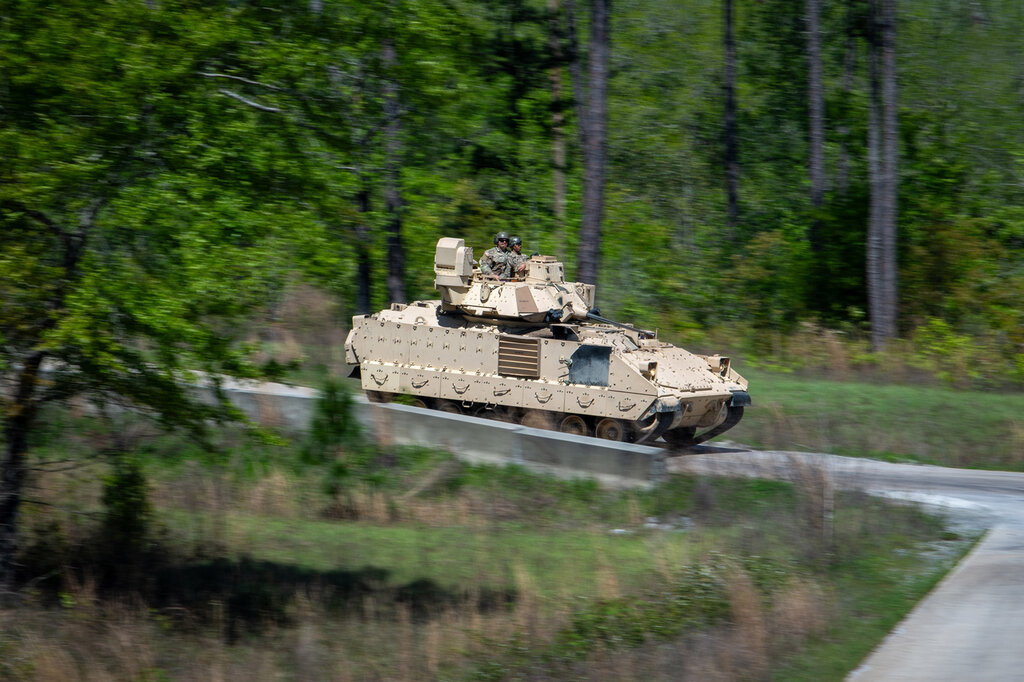
The US Army’s Bradley fighting vehicle could be replaced by a hybrid-engine platform under the OMFV programme. Credit: US DoD
At a theoretical level, the increased torque offered by an electrified vehicle is a benefit for military applications. However, the technology brings with it new design challenges that can introduce risk into a programme.
For instance, the electric motors and power converters in a Prius must cope with a consistent and low range of vibration and shock. A military platform will exhibit high levels of vibration and shock, especially if off-road, as well as challenging environmental conditions like extreme cold and heat.
This can be mitigated by using induction as opposed to permanent magnet motors but is indicative of how the HED design process must be altered for AFVs.
Experiments and trials
There are multiple efforts underway to developed HEDs and hybrid electric vehicles. Germany’s FFG revealed the Genesis 8x8 HEV in 2020, which the company stated was a technology demonstrator designed to prove and develop the hybrid drive technology in anticipation of requirements for the European Main Ground Combat System (MGCS) tank programme.
It employs a fully hybrid system with a diesel electric generator, and eight in-wheel motors that provide permanent all-wheel drive. Steering, braking, and acceleration are all controlled through moderating the RPM at each wheel station. Each wheel generates 171 kW of power for a vehicle total of 1,368 kW and 15,622 Nm of torque.
Current indications are that the MGCS will indeed include a HED, but specifics are not known.
This could bring several benefits to the vehicle design; the Genesis demonstrator is indicative of how power can be changed at each wheel hub through software. It also demonstrates how much space can be saved by using electric motors and the design simplicity that results from not having to factor in a mechanical transmission and drive train.
When conventionally driven vehicles are required to perform off-road, they are typically fitted with a relatively large transmission. This enables the vehicle to produce the very high levels of torque required to overcome rolling resistance and climb obstacles.
However, a transmission adds a lot of weight, and takes up a lot of space. A complete AFV powerpack can occupy as much as 38% of the vehicle’s volume, the transmission will contribute significantly to this. For example, the RENK HSWL 256, used in the Puma IFV, weighs 1,700kg and has a total volume of 971 litres. Compare this with QinetiQ’s E-X-Drive, which weighs 400kg and has a total volume of 112 litres, indicating a reduction of 76% in terms of weight and 68% in volume.
This potentially means for more space for combat equipment and systems, or a reduction in the space that has to be armoured, which in turn can lead to reduced vehicle weight and improved mobility potential.
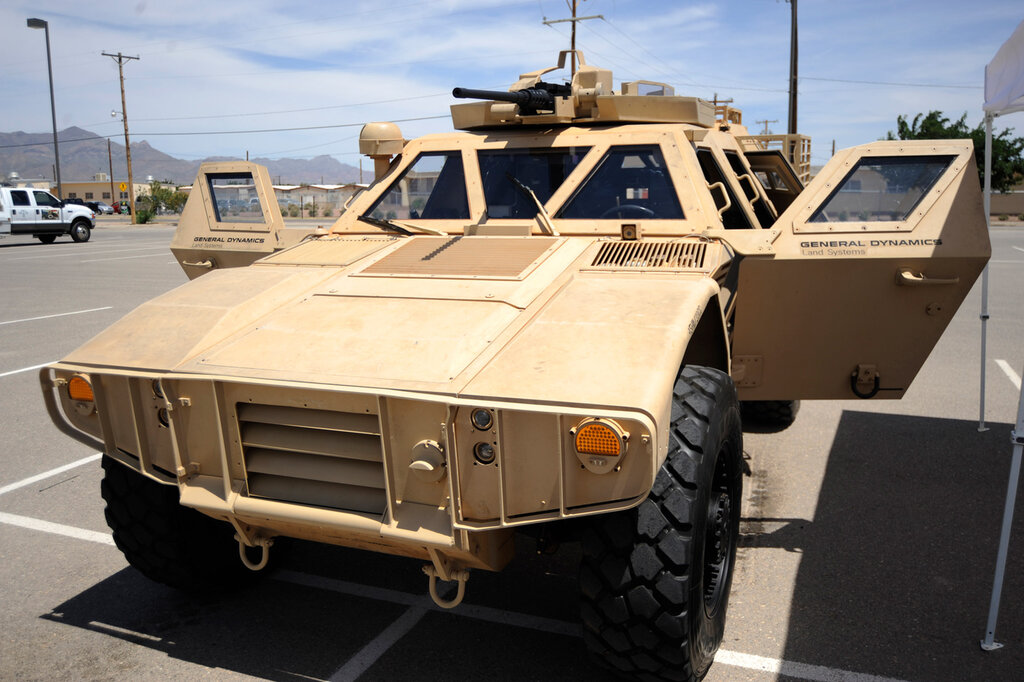
In 2010, the US Advanced Ground Mobility Vehicle demonstrated a tactical vehicle that was hybrid-electric capable with in-hub electric drive. Credit: US DoD
Nonetheless, Allison has developed its eGen Force hybrid propulsion system for tracked AFVs, which is rated for 50-ton platforms but can be expanded to 70 tons if required. It uses parts from the existing Abrams X1100-3B1 transmission and generates 220 kW of power for a parallel hybrid vehicle.
Allison was contracted by the US Army in August 2022 to deliver a sub-system based on the design for testing. In the US, the Optionally Manned Fighting Vehicle (OMFV) is expected to carry a hybrid drive train, and this is partly the reason for the Allison contract.
The AbramsX, also presented in 2022, includes a hybrid electric drive to improve its fuel performance over the original Abrams, however, it is also likely to be useful in powering the many mission systems that the vehicle is expected to carry.
The UK has also initiated trials of hybrid technologies on its Foxhound, Jackal, and Man SV vehicles. The vehicles were retrofitted with HEDs, and the Foxhound was designed to have its drive train replaced with a HED if required.
The ability of a vehicle to provide off-board power in support of dismounted units is also valuable to commanders and medical staff who must also deploy extensive suites of mission systems and communication systems for perform their role. HED also offers the greatest potential for fuel savings when applied to logistics vehicles like the Man SV.
Exploring the benefits
The technology is ideally suited to operating at a set speed for long durations, which returns the greatest range for the spent fuel. This is a more typical duty cycle for a logistics vehicle, which will be expected to complete multiple road journeys per day. This is an important area for military HEDs; logistics vehicles are necessary, but the heavier they are, the more fuel they will generally consume, which increases the need for logistics vehicles to carry that fuel.
Consider, for example, the impact on fuel requirements of transporting the UK’s Ajax reconnaissance vehicle at 42 tonnes, compared with the 12 tonnes of the Scimitar Mk 2 that it replaces and the additional burden that transporting that weight, multiplied across a fleet of vehicles, will place on the British Army’s logistics network. In that context, the benefits of reducing fuel consumption of the vehicles needed to transport those vehicles is a straightforward and beneficial choice.
Hybrid electric drives appear to offer a range of benefits to AFV fleets, from mobility, to space, weight and power, as well as the potential for a reduced logistics burden. It stands to reason that as these benefits are socialised and the technology de-risked through further commercial and military exploration, that widespread adoption will follow.

AI could harness commercial satellites to improve battlefield communications. Credit: Vector illustration Who_I_am via Getty.
So, these kinds of decisions, which human beings had to do - and human beings, of course, are very intuitive - that intuition also gets embedded with AI machine learning.
Dr Rajeev Gopal, vice president for Advanced Programmes at Hughes.
Australia could be one of the main beneficiaries of this dramatic increase in demand, where private companies and local governments alike are eager to expand the country’s nascent rare earths production. In 2021, Australia produced the fourth-most rare earths in the world. It’s total annual production of 19,958 tonnes remains significantly less than the mammoth 152,407 tonnes produced by China, but a dramatic improvement over the 1,995 tonnes produced domestically in 2011.
The dominance of China in the rare earths space has also encouraged other countries, notably the US, to look further afield for rare earth deposits to diversify their supply of the increasingly vital minerals. With the US eager to ringfence rare earth production within its allies as part of the Inflation Reduction Act, including potentially allowing the Department of Defense to invest in Australian rare earths, there could be an unexpected windfall for Australian rare earths producers.
Total annual production

$345m: Lynas Rare Earth's planned investment into Mount Weld.

Phillip Day. Credit: Scotgold Resources