Manufacturing
3D printing: where next for additive manufacturing in defence?
The potential for additive manufacturing - also known as 3D printing - has been recognised for several years, but while printing technologies and processes continue to mature in the commercial sector, technical and institutional challenges still need to be overcome for wider adoption in defence manufacturing. Grant Turnbull finds out more.

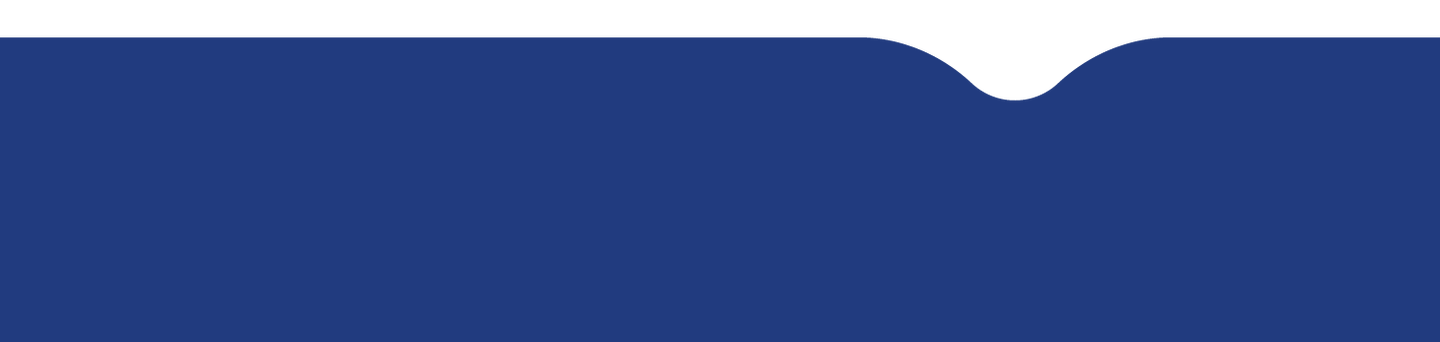
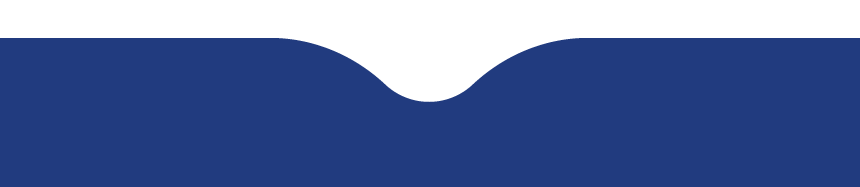
Industry analysts have talked about the disruptive nature of 3D printing for several years, and the benefits of being able to print parts on demand for manufacturing or supply chain purposes are well documented. In reality, however, companies still mostly rely on traditional manufacturing methods for parts, particularly subtractive CNC machining, and 3D printing is so far only used for early development stages and complex parts.
For much of the 2010s, the idea that end-users could print parts when needed - reducing the cost of storing parts and increasing availability - did not see any significant adoption beyond pilot programmes and research projects.
According to Deloitte, 3D printing entered a “trough of lowered expectations” by the mid-2010s and only began to see growth again by around 2017. Now, in its latest technology predictions report, the consultancy sees a return to healthy growth for the 3D printing market, with sales surpassing $2.7bn this year, and topping $3bn by 2020 - equating to double digit percentage annual growth.
This growth is being attributed to the growing number of materials that can now be printed, at a quicker pace to reduce lead times, and with larger dimensions. “The list of possible 3D-printable materials has expanded to more than double what it was five years earlier, and mixed-material printers are becoming more common,” said the Deloitte report. “The biggest shift in this regard has often been away from plastic and toward metal printing.”
Tailoring 3D printing tech for defence
Manufacturers, defence organisations and military end-users are continually assessing how 3D printing can be used to decrease costs, increase the pace of development, and strengthen supply chain resilience. A 2018 study of additive manufacturing by the European Defence Agency (EDA) noted that manufacturing costs can be reduced for initial production batches or when production batches are small or highly personalised (including parts with complex geometries) for a specific role.
The EDA, however, identified several challenges that remain with 3D printing, particularly in manufacturing. “It should be borne in mind that traditional precision manufacturing technologies such as CNC machining are generally at least one order of magnitude superior to additive manufacturing technologies,” the study noted. “Even the most well-known and developed of the current [additive manufacturing] technologies are not suitable for applications requiring very precise and fixed tolerances.”
Other technical challenges also exist, particularly when 3D printers are connected into a wider network, also known as the Internet of Things. Hackers with malicious intent could steal designs and even compromise parts through modifying source files.
“European research organisations and industrial players will investigate the potential of 3D printing technologies for producing future explosives and propellants.”
Nevertheless, organisations such as the EDA continue to explore the different avenues that 3D printing offers. In December 2018, six participating EDA member states - Finland, France, Germany, Netherlands, Poland and Sweden and Norway - signed an agreement to work together on the Additive Manufacturing Techniques for Energetic Materials (AMTEM) project.
With France acting as lead nation, 15 European research organisations and industrial players will investigate the potential of 3D printing technologies for producing future explosives and propellants.
The AMTEM project was officially launched in March 2019 and will carry on for another four years to assess appropriate materials and related 3D printing techniques. The vision is that these new techniques could lead to new types of warheads and propellants with enhanced performance, while at the same time ensuring faster and cheaper production for small batches and rapid prototyping. This could also be expanded to develop new munitions and missiles concepts with increased operational performance.
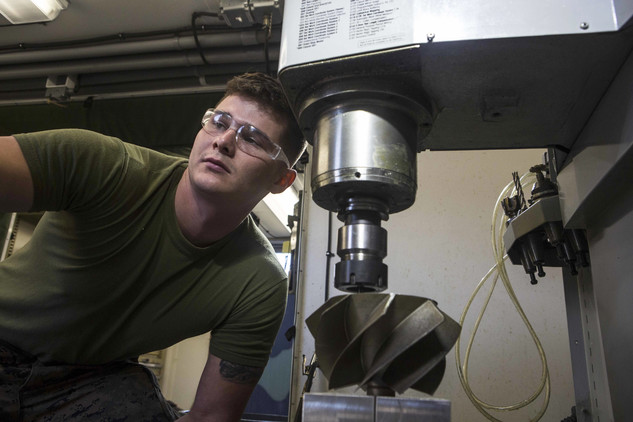
The US Marine Corps successfully trialled 3D printed parts on its M1A1 Abrams tanks. Image: USMC
3D printing on the frontline
Additive manufacturing is seen as particularly important for units that are deployed on operations, particularly where units are in remote locations that are difficult to supply by sea, road or air.
The US Marine Corps is one force that regularly finds itself deployed to the far reaches of the earth, where there is little infrastructure and receiving parts can take several weeks, if not months, which translates into equipment being unserviceable and out of action.
It’s no surprise then that the USMC is exploring several ways it can use 3D printing to improve operational readiness and mission effectiveness. In January, the service announced that it had successfully trialled 3D printed impellers on several of its M1A1 Abrams tanks, conducting around 100 hours of qualification trials. The corps now plans to use 3D printed parts when original parts wears out and a replacement cannot be sourced quick enough.
“Call it a spare tire or a stop-gap solution,” said Joseph Burns, technical lead for Marine Corp Systems Command’s (MCSC) Advanced Manufacturing Operations Cell, in a USMC statement. “This can get you through a mission, through your training exercise or whatever may be critical at the time.”
“In April, it was announced that a USMC F-35B had flown with a part that had been 3D printed by the unit’s combat logistics arm.”
An impeller effectively removes dust from the Abrams’ engine to keep the filters clean, which if not functioning correctly can degrade the tank’s performance. MCSC is now creating a 100-page technical data package, with the first version expected shortly and full qualification soon after.
Burns noted that 3D printing the impeller is a more expensive option, although that is offset by the rapid pace that a part can be delivered.
The 31 Marine Expeditionary Unit (31 MEU) - a permanently deployed force - has also used 3D printers as an alternative, if temporary source for parts. In April, it was announced that a USMC F-35B had flown with a part that had been 3D printed by the unit’s combat logistics arm. This was a relatively small and simple plastic bumper for the landing gear door, but the alternative would have been a time-consuming and expensive replacement of the entire door assembly.
The unit also developed a 3D printed lens cap to protect the expensive camera on ground robots that the unit has also deployed. The templates for both parts will now be available to any other unit that may have similar requirements in the future.
While 3D printing still has several technical challenges to overcome that would make it an economically better option than traditional methods, the benefits that can be had from adopting the technology is proving to be difficult to resist for those either manufacturing equipment, or those on the frontline that need parts quickly to retain operational effectiveness. Expect to see yet more innovative uses of this technology in the future.
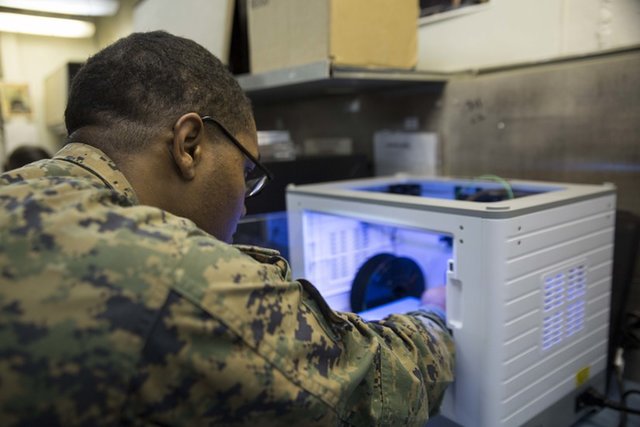
The idea of units being able to print parts, rather than waiting for deliveries to the frontline, is appealing to the military. Image: USMC