INTERVIEW
Talking business: Babcock on Type 31, digital twins and more
Berenice Healey catches up with Babcock's engineering director for warships Ian Cowper to discuss the Type 31 programme, integrating digital technologies into naval shipbuilding and through-life support, and the company’s plans for the near future.
Berenice Healey:
What’s the latest on the Type 31 design and build programme and what are your aims for it this year?
Ian Cowper
Babcock is leading Team 31 to deliver five Type 31 frigates for the Royal Navy. Driven by innovation and backed by heritage, the Arrowhead 140 general-purpose frigate is a modern technology-enabled warship that will meet the maritime threats of today and tomorrow.
Type 31 will be at the heart of the Royal Navy’s surface fleet, deterring aggression and maintaining the security of the UK’s interests. A truly state-of-the-art warship, the modular, scalable and proven design has been engineered to minimise through-life costs.
Assembled at Babcock’s Rosyth facility, the programme will maximise social value throughout the UK maritime supply chain. Over the last decade, Babcock’s Rosyth facilities, which are home to one of the largest waterside manufacturing and repair facilities in the UK, have seen significant investment into transforming the site into the UK’s most modern maritime support facility.
Digital transformation is at the heart of the site’s growth – this is not just a vision for the future but made a reality through the Type 31 frigate programme where further investment in facilities and manufacturing equipment is supporting the integration of technology and new working practices, creating a dynamic, effective and efficient, digitally enabled facility.
Investment includes the installation of additional advanced manufacturing capability and the construction of a new assembly hall capable of housing two Type 31 frigates for parallel build and assembly activity. Panel lines will support state-of-the-art automated manufacturing acting as a key pillar for Rosyth’s digital facility strategy and creating a cultural shift in the manufacturing process.
On the Type 31 programme, the steelwork frame for the new assembly hall is now complete with its cladding now being applied. All major and long-lead supply chain contracts have been placed, to date representing almost a third of all contracts and nearly 80% of the value.
Steel will be cut to begin construction of the first Type 31 by end of 2021.
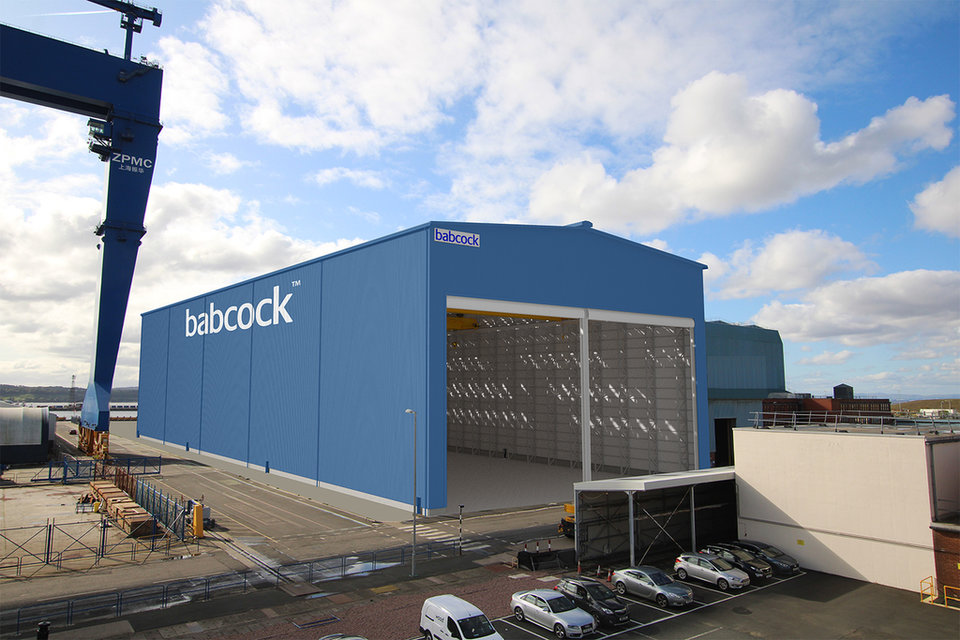
// Artist's impression of Babcock's new assembly hall for the Type 31 programme.
How is Babcock using digital communications, including in the support environment, and incorporating technology such as augmented reality?
Our approach to integrating digital and data technologies is iSupport360. Deploying advanced analytics helps us to solve complex challenges and to be proactive and lessen operational risk through predictive maintenance modelling. The range of technologies we use in our through-life support to the Royal Navy includes artificial intelligence, virtual reality robotics, digital twins and autonomous survey techniques all complemented by investment in infrastructure and the digital skills of our people.
This has been a key enabler in the Type 31 design and build programme and the Type 23 frigate life management plan, which sees the transformation of the ships into digital platforms through some of the largest capability upgrades and updates enhancements since build.
Through iSupport360 Babcock is using digital communications as part of a collaborative approach, integrating people, processes and technology to enable mobile, remote and connected working.
An example of how this is being implemented in the support environment is the installation of secure Wi-Fi networks onboard ships in upkeep. This allows us to unite traditional engineering with cutting-edge technology to drive efficiencies and improvements at the point of work, which leads to a complete understanding of the asset and added benefits for our customers.
Implementation of a secure local long-range wide area network is also enabling a range of internet of things devices, including live asset location tracking and management, environmental monitoring of confined spaces, and safety monitoring for fire zones and restricted areas. Upkeep is a non-operational period and these secure Wi-Fi/Li-fi networks are removed and the platform certified clear of potential cyber threats before being handed back to the authority.
Shore support for deployed ships’ systems and the implementation of digital twins will depend upon the speed and efficiency of getting data back to the support organisation so that the fleet-wide analysis can be undertaken. Currently, through a Ministry of Defence and Babcock trial, this is being achieved through data downloads from the ship to the shore side technical authority, enabling the data to be transformed into real-time support decision information.
How is Babcock using digital twin technology with naval programmes, for example, the Navy’s 4.5” gun?
Babcock has taken the concept of the digital twin to improve and assure the availability, reliability and required performance targets of ships’ systems.
We have developed the technology through several iterations of varying complexity, beginning with the installation of sensors on a frigate’s chilled water equipment – monitoring heat, pressures, fluid flow, ambient data , and so on – to taking data directly from a frigate’s machinery control system – circa 300 lines of data – to provide a system-level view. The data is then processed to enable scenario testing and failure prediction, thereby informing the appropriate maintenance interventions.
The concept and algorithms behind these developments have been a resounding success and lay the foundations of a step-change in the provision of through-life support through effective exploitation of the digital thread.
iSupport360 enables us to improve the availability and readiness of assets whilst also reducing through-life support costs but, most importantly, the capability also enables us to recommend and optimise predictive support interventions against known risk.
Babcock’s investment in technology, digital processes and our people skills means we can support customers with more informed and advanced decision making. That, along with our technical authorities drives efficiency and value to meet the operational and support challenges.
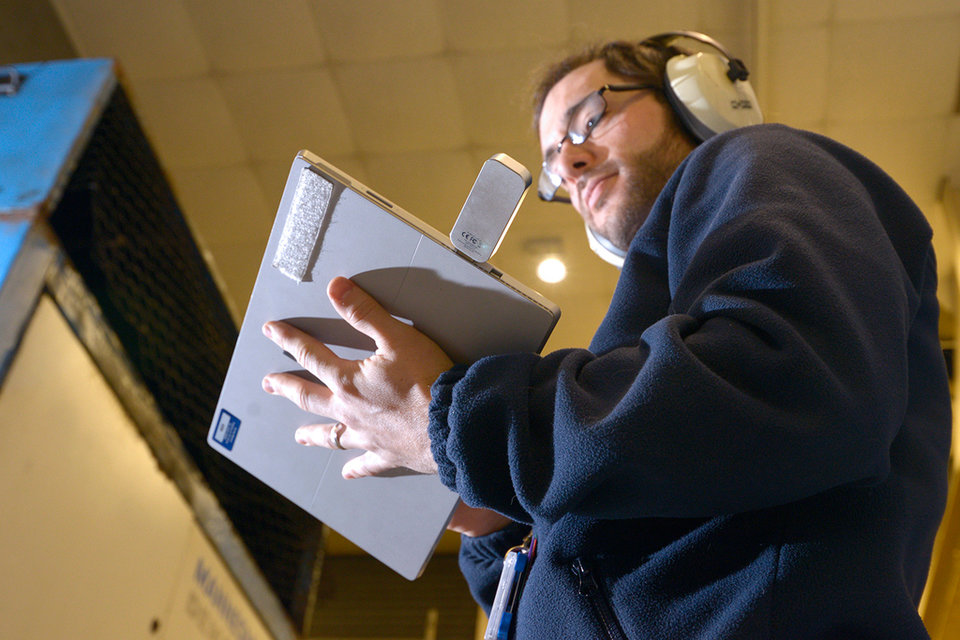
// Babcock ues its iSupport360 system to enable mobile, remote and connected working.
Sustainability is now a key focus for the defence industry. What is Babcock doing to minimise its impact on the environment?
The road to zero carbon and the need to decrease carbon-based fuel consumption also drives a requirement to optimise the use and maintenance of main engines. This goal is currently being realised through innovative technologies and Babcock’s introduction of monitoring and predictive analytics and prognostics, thereby improving maintenance intervention planning. Sustainability is at the heart of what we do, and the company is focussed on a carbon-neutral strategy.
The Covid-19 pandemic has had a huge impact on personnel everywhere. How is Babcock working to support its workforce of the future?
Since the start of the pandemic, Babcock has continued to support its customers’ programmes throughout its sites. There has been an unwavering focus on creating safe working environments through a range of measures such as PPE, Covid-19 testing, social distancing and the adherence to strict protocols to protect our people and our customers’ programmes. Allied to this was the fast mobilisation of employees to work at home where they could.
This was successfully done in a short timeframe through providing home working equipment such as furniture, hardware and software, upgrading and introducing new communications channels and tools such as Microsoft Teams, an SMS messaging service, an employee portal and a mobile app.
A major emphasis also continues to be placed on health and wellbeing, encouraging employees to keep connected to colleagues and their line manager with the promotion of agile working supporting the needs of the business and helping to create a positive work/life balance.
Babcock has welcomed more than 590 graduates and apprentices to its global business as part of the 2020 intake. This included 259 graduates and 338 apprentices on sites all over the world working on a variety of projects. Our 2021 recruitment for the next-generation talent pipeline is already underway.
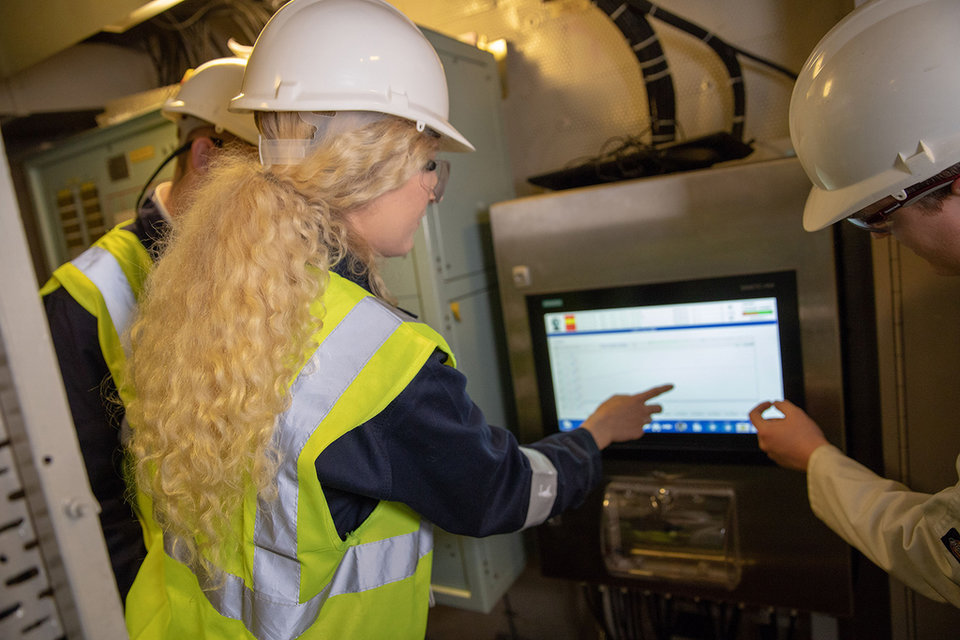
// Onboard maintainers at work.
Are there any other developments you would like our readers to hear about?
Delivering warship build and support is exciting, not least as we embark on the new challenges of global support and Carrier Strike Group deployments and the need to increase fleet availability due to the operational tempo, whilst reducing support costs.
So, whether it is transactional, through-life support, contracting for availability or contracting for capability commercial models, the common factor is the need for an increased understanding of the material state of the asset and systems of systems performance to accurately predict failures and targeting the right intervention at the right time.
To address these challenges, we have focussed on gathering, analysing and transforming the data into decision-support information that is dynamic against actual operational feedback. Of course, the best person to understand the material state is the on-board maintainer to gather the insight enabling the technical authority shoreside to provide the foresight and this is working extremely well within our class output management through-life support teams which is industry-led with integrated Royal Navy teams embedded providing the deep support and operation experience and capabilities.
At Babcock, innovation isn’t just in the cutting-edge technology we work with, it’s in our people, it’s in our partnerships and it’s what we deliver.
// Main image: Artist's impression of the Type 31. Credit (all images): Babcock
The UK Ministry of Defence’s recent Integrated Review and Defence Command Paper reaffirmed its commitment to naval power and UK shipbuilding. One company front and centre of supporting Royal Navy programmes is Babcock, which is leading the team to build the Type 31 frigates and provides naval support services using advanced technology including augmented reality and digital twins.
We caught up with Babcock's engineering director for warships, Ian Cowper, to chat about ongoing projects and the latest in naval shipbuilding and through-life support technology.