“Most of the wars in the last few hundred years were won, or lost, due to logistics,” says Ron Ben-Zeev, founder of World Housing Solutions (WHS), a Florida-based company with an innovative approach to expeditionary buildings that is already helping to simplify that supply chain burden, and save energy and lives in the field.
According to official Pentagon statistics, a staggering 58% of combat casualties during operations in Iraq and Afghanistan were linked to logistics and of those, some 80% were said to be transport related. With widespread recognition that the ongoing trend of each conflict being more hungry for energy and resources than the one before it is simply unsustainable, the time has come to cut back on the logistic tail like never before and slash the numbers of troops lost to death and injury as a result.
Ikea meets construction: Rapidly Deployable Systems
Ben-Zeev explains that historically there have been three main conventional options available to the military when it comes to building Forward Operating Bases (FOBs) – tents, containers and plywood construction. All of those – even tents – require flat, graded terrain and that involves, bulldozers and earthmoving equipment, time, valuable energy and significant logistical effort to achieve. It also requires personnel with specific construction skills too.
WHS takes a different approach, fielding portable structures that can be put together quickly and efficiently on ungraded ground, by almost anyone – “Ikea meets construction”, as Ben-Zeev puts it. Able to be carried by no more than four soldiers, the Rapidly Deployable System (RDS) components can be pre-fabricated in the factory to meet particular needs, and come with hugely superior energy-saving performance built in, which has become an increasingly important consideration for the 21st Century military. Quieter, more sustainable bases are not just more efficient, they are safer and more survivable too.
Foam core composites: tailored expeditionary solutions for America’s armed forces
The company was started just over six years ago, and initially the aim was to help solve the world’s humanitarian refugee problems by developing composite shelters that could be quickly delivered and built as they were required. Along the way, that work drew the attention initially of the US Navy, leading to WHS first working to develop prototype structures and then ultimately to providing tailored expeditionary solutions for America’s armed forces in general.
Today, that encompasses a wide range of buildings, including joint and tactical operations centres (JOCs/TOCs), mobile command & control, field medical facilities and mobile hospitals, emergency decontamination shelters, mess halls, accommodation, offices, guard houses, latrines, warehousing and recreational facilities.
“A 640 square foot structure can be assembled by 10 men in less than six hours, without power tools or heavy equipment.”
At the heart of the system lie WHS’s proprietary structural composite panels, encompassing different kinds of foam cores depending on the specific end application, which can be made up to 12 inches (30cm) thick for outstanding thermal efficiency – and can be armoured too. It makes for an extremely long-lasting material that calls for very little in the way of resources to be put together. A 640 square foot structure can be assembled by 10 men in less than six hours, without power tools or heavy equipment, while a simple guard house can be up and ready in just 20 minutes.
Whether mounted on a conventional slab or one of the company’s unique, fully adjustable platforms, the finished RDS structures are termite, mould, mildew, rot and fire resistant, can cope with earthquakes and hurricane force winds of up to 155mph and with a minimum of 15 years of useful life, can be disassembled and redeployed again and again.
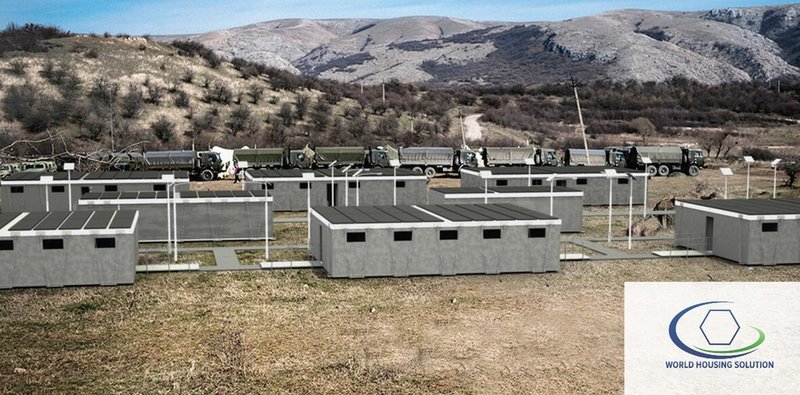
A camp of Rapidly Deployable System buildings taking shape. Image: World Housing Solutions
Lean and green: lowering indicative fuel costs
Arguably the biggest benefit, however, is the unparalleled reduction these structures yield when it comes to the logistics burden imposed by the fuel required for heating or cooling, and the associated loss of life along the supply chain. According to independent studies, WHS buildings are the only expeditionary structure solution that yields an actual return on investment, with an RDS standard deployment complex having indicative fuel cost of less than a sixth of a comparable conventional tent equivalent.
“Even if you are not an expert you can figure out that 50 tons of air conditioning will use more electricity and power than six tons,” Ben-Zeev says. “That is the difference between our rigid wall latrines and tent latrines. More World Housing Solution rigid wall structures means less fuel, which means less generators which means less energy wasted and more safety for our troops and, also, for our planet.”
Living in a Yeti cup: ‘R’ values and $95m savings
One of the most convenient ways to consider a building’s thermal insulation is by means of its ‘R’ value – a measure of its resistance to the transfer of heat through its fabric – and the higher the number, the lower the heat loss. A typical US house, for example, has a value of less than R-10. An average WHS expeditionary structure, by contrast, would be around R-30, while the panels can be made to achieve a thermal resistance in excess of R-72 if required, and as the company’s founder is keen to emphasise, that is a whole building value, with proprietary panels being used for the roof, walls and floor.
“That means that yes, you are basically living in a Yeti cup,” he says. “It takes very little energy to cool or heat something that is that thermally efficient. That is why, when twinned with hybrid energy technology such as solar and batteries, we can achieve savings, over the lifespan of a base for 250 men, of more than $95M, depending on the cost of fuel and the location of the base.”
Evolution of solutions: alternative energy, potable water and sewer solutions
The WHS expeditionary portfolio also includes alternative energy, potable water and sewer solutions, with small-footprint modular water filtration and purification systems and sewage treatment units that can service as few as five soldiers, or support up to 6,000. Designed to take fresh water from sources such as existing municipal supplies, constructed wells, rivers, streams or lakes, the low-maintenance system removes the common potentially harmful contaminants including iron, nitrates and manganese, reduces turbidity, and can function from desert heat to temperatures well below freezing. On the sewage side, the high-performance treatment system produces low sludge volumes, ensuring minimal handling and low disposal demand.
For millennia, throughout the long history of warfare right up to the recent conflicts in Iraq and Afghanistan, the military has routinely camped under cloth – but it seems times are now finally changing for forward-deployed soldiers. Billed as ‘the evolution of expeditionary solutions’ these new buildings offer levels of comfort and safety that would have been unimaginable for those countless previous generations of warriors, deployed far from home, and as Ben-Zeev puts it, “a more comfortable soldier is a better fighting soldier.”